For a more detailed version of this story, including how our partners at KTA-Tator identified the problem, see the article in CoatingsPro Magazine.
When any facility is being converted for a new use, problems with renovating or upgrading the concrete floor can deliver a surprise if the building’s previous history isn’t fully known. The resulting failure in the floor coating system is infuriating for both applicator and owner, and – as in this case – they won’t have a clue as to why.
The lesson: it’s critical to learn as much as you can about the floor and its former uses before you begin applying coatings. This was a floor coating lesson learned the hard way. Fortunately, it has a good ending.
CFI helped by jumping right in to help their experienced customer get the owner’s floor up and running when just such a failure occurred.
The Job
This lesson was learned by a major national contractor and the coatings subcontractor tasked with converting a former industrial building into a marijuana growing facility. When bubbles appeared in the newly coated floor, CFI was called onto the project, and through some proactive investigation and old-fashioned customer service, helped save it from disaster.
The facility in question was a 50,000 square-foot building that stands on a hillside in an industrial park in the Mid-Atlantic region of the U.S. Beyond having a former life represented by the commercial real estate broker as “light manufacturing,” little was known about the building’s former uses.
The owner hired a major national general contractor to lead the renovation and build-out of the facility, converting it to serve the growing demand for CBD (cannabis) products, which have recently been legalized in many states. The contractor retained a highly experienced coatings subcontractor to provide a CFI resinous coating system on the concrete floor.
Uncharacteristically, the surface preparation had been done previously by the general contractor. The coatings subcontractor typically does his own surface prep work, as it allows him to be sure it was done correctly as well as learning as much as possible about the condition of the floor prior to coating application. coated.
It was a red flag, but the coatings subcontractor weighed his options of arguing with a huge GC and determined that the size of the job outweighed the potential risks.
The general contractor informed the flooring professionals that the floor had been tested for moisture and the result was 10 pounds moisture vapor pressure (MVP) in 24 hours. That’s well above the 3 pound limit that an ordinary primer can handle.
Based on that information, the subcontractor bid the coating system using CFI’s WearCOAT 1080 Moisture Mitigating Primer, which has been tested to hold back MVP as high as 16 pounds.
The specification also included CFI’s WearCOAT 440 100% solids epoxy mid-coat. This system is designed to easily handle such an industrial job with light to moderate foot and wheeled traffic. Both the primer and epoxy coating were applied with no issues.
The Problem
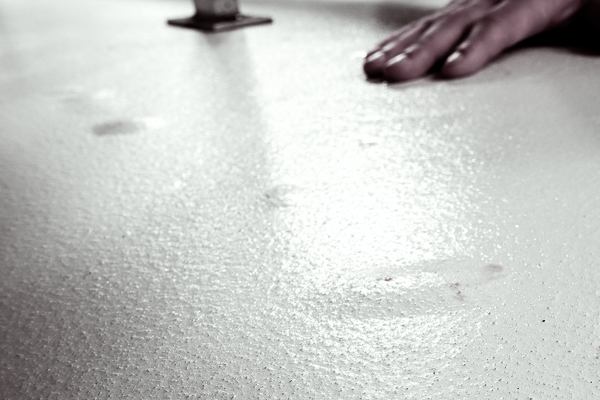
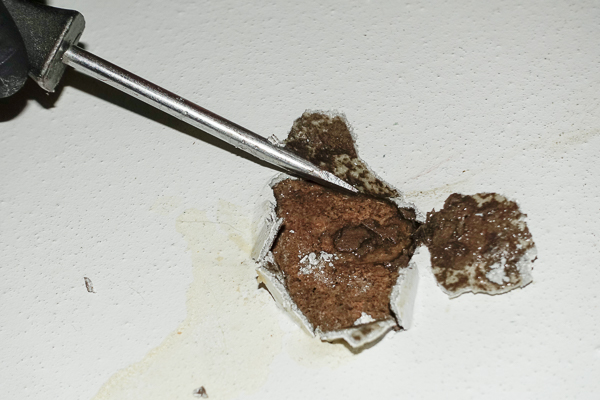
Lurking beneath the coating was an unforeseen problem for everyone.
About four weeks after the job was completed, bubbles began to appear in the floor in certain areas. Called in to inspect it, the flooring subcontractor found some of the bubbles leaking brown liquid that appeared to be pushing up through the coating.
Clearly, the floor had more problems than just increased MVP, and the combination of that and likely contaminants meant this job was going to be difficult – and expensive – to deal with.
The discovery of the brown liquid and the problems it was causing in the floor sent tensions high. The building owner had the GC under a tight completion deadline to get the building operational and placed blame on the coating subcontractor, even implicating that CFI might also be at fault.
The liquid that oozed from beneath through the bubbles of the resinous floor coating was brown with telltale rainbow colors of oil on top of water. The owner and general contractor assumed the messy liquid was somehow caused by the coatings.
The subcontractor, needing to avoid a very expensive re-grind and re-coat, really needed to prove this was not the case.
The Fix
Without hesitation, CFI sent a representative to the job who took photos and samples of both the applied coatings and the brown ooze. At its expense, CFI asked KTA, a nationally respected independent forensic coatings lab, to analyze the coatings and what was bubbling up from beneath the surface.
Using chemical and spectrograph analysis, KTA reported that the ooze was ground water contaminated with machine oil. It also reported no anomalies with the coating. Separately, the facility owner contracted for similar testing and was given the same results.
The contractor, with the help and support of CFI, did not allow himself to be made a scapegoat for an issue where he was not at fault. CFI stood with the coating contractor, even helping with costs for independent testing. It’s just an example of how CFI partners with its customers.
The Results
The building owner, anxious to get the marijuana growing facility up and running, realized he could not blame the contractor or CFI for the problems with the floor. Further, the owner saw that the contractor – and CFI – were serious about fixing the actual problem, rather than assigning blame. He asked the contractor to fix the bubbling floor and paid him for the additional work.
CFI’s tech team worked closely with the contractor, specifying a completely different coating system designed for such challenged floors: WearCOAT 490 primer, and WearCOAT 491 for the topcoat. These products are designed to work with moist and moderately contaminated substrates.
It’s now been several years since the repairs were completed and there have been no further problems. The facility owners are happy, as – well, ahem – likely, their customers, as well.
The Lesson
The lesson both the building owner and contractors learned – and that every contractor should consider – is to always know what you are over coating, and wherever possible, do your own surface preparation.
The contractor is a veteran of concrete floor coating industry, and normally follows that best practice. This time, he didn’t, and it prevented him from inspecting the slab prior to preparation, which may have shown the oil stains from decades of being used for a machine shop.
Another factor is the building’s location on a hillside, which meant rainwater had run along and underneath the building for decades. This is the likely source for the increased MVP.
At CFI, we are always happy to help contractors out of tough situations. More importantly and wherever possible, we help our customers prevent problems from happening in the first place. If you need help with your next coating job, contact our Customer Service or call +1-215-723-0919.